

The striker was 0.787 kg in weight and had a hemispherical geometry shape, with a tip radius of 5 mm. Tests were performed using a drop weight testing machine on different sample thicknesses to achieve different impact responses. It shows that glass fiber type E-800 g/m 2 produced much thicker laminates compared with type C-600 g/m 2 for the same number of plies. This is because the same procedure has been used to fabricate all the specimen. The standard deviation were the same because the thickness of the fabricated specimens is almost the same. The thicknesses were measured after the curing process. Table 7.2 compares the average thicknesses of the laminates. In this test, the projectile velocity range is within 70–240 m/s. The speeds of the projectiles are varied using the gas gun. In this test, specimens with dimensions of 100 mm × 100 mm were impacted with three types of projectiles: blunt, conical, hemispherical. High energy impact tests were carried out using an SSGG at the Faculty of Manufacturing Engineering, Universiti Malaysia Pahang. Specimen plates with a size of 100 mm × 100 mm for both types of glass fiber were cut using a CNC router machine.
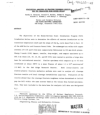
For the high velocity impact tests, GFRP type E-800 g/m 2 and type C-600 g/m 2 were fabricated into four different thicknesses, 6 mm, 8 mm, 10 mm, and 12 mm. The epoxy resin and hardener used were from types Zeepoxy HL002 TA and Zeepoxy HL002 TB. The process of preparing the compound was based on a 2:1 ratio, that is, two portions of epoxy to one portion of hardener by mass. The materials were fabricated using a hand lay-up technique with the aid of a hot-press machine. These woven roving materials were laminated with epoxy resin to increase their impact strength. The composite materials chosen are woven-roving GFRP type C-600 g/m 2 and type E-800 g/m 2. Mohammad Jawaid, in Durability and Life Prediction in Biocomposites, Fibre-Reinforced Composites and Hybrid Composites, 2019 7.4 Experimental procedure for damage detection
